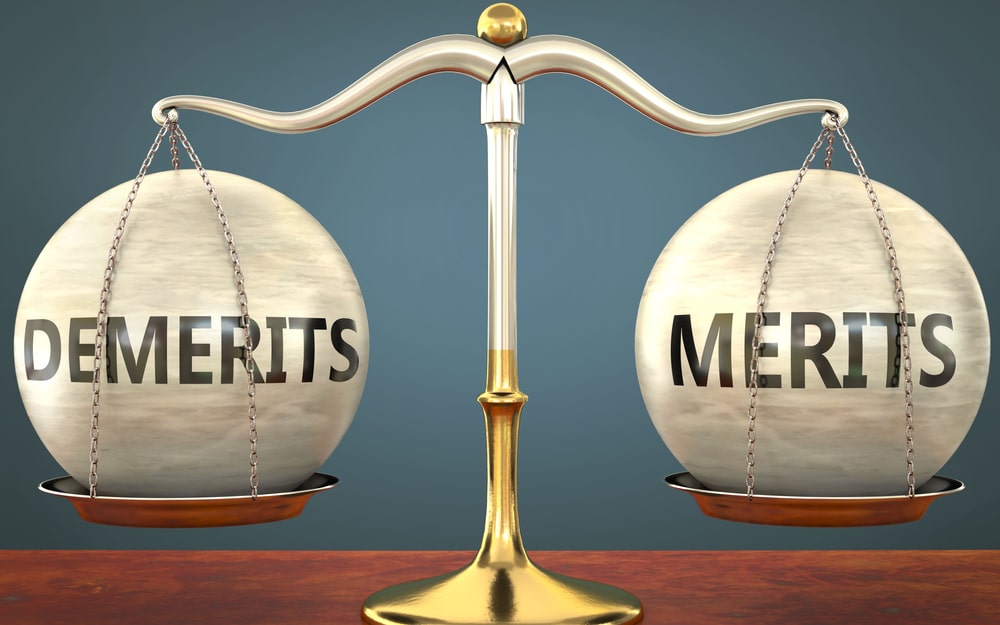
商品を購入して不具合があったとき、顧客はどのように企業に報告するかご存じですか。商品を送ったり、パッケージや商品に記載されている番号などを伝えたりします。そして、世の中の多くの商品は、ロット番号やシリアル番号などにより管理されています。今回は、管理方法のひとつであるロット管理について解説するので、参考にしてください。
ロット管理を行うメリット
まず、ロット管理とは製品に割り当てたロット番号により管理をおこなう方法のことです。製品の製造から出荷、販売後のサポートまでを円滑におこなうため、一元管理をする際に有用となります。同じ条件のもとで製造される一定数のグループをロットと呼び、1ロットをどれほどの数にするかは企業や製品ごとに適切な量を選ぶ必要があるのです。これに対して、製品ひとつひとつに番号をつけて管理する方法はシリアル番号管理と呼びます。
よく、シリアルナンバー入りの数量限定商品などにプレミア価格がついたりしています。これはごく少数しか生産されておらず、同じシリアル番号のものが世界にひとつしかない唯一無二の商品であることが理由です。
ここからわかるように、ロット管理=一定数の製品をまとめてナンバリングして管理する方法、シリアル番号管理=ひとつひとつの製品を個別にナンバリングするもの、ということです。ロット管理をおこなうメリットは、大きく分けて3つあります。
製造量を管理しやすくなる
ひとつめは、製造する量を管理しやすくなることです。ロットごとに管理することで、過剰に製品を作ることを防ぐことができます。そもそも1つのロットに設定する量は、生産コストや顧客の需要などを軸にしています。このロットを適切に管理することで計画を立てやすくなり、適切な量での製造がおこなえるのです。品質管理がおこないやすくなる
2つめに、品質の管理がおこないやすくなることが挙げられます。同一条件下で製造されたものを同じロット番号に割り当てるため、とある1商品に問題があった場合「いつ製造されたものなのか」「どのような工程で製造されたものなのか」「同じ問題のある商品があといくつぐらいあるのか」といった予想がしやすくなります。大量にある商品を、シリアル番号のようにひとつひとつ番号を割り当ててしまっては管理が追い付きません。そこでロット管理することで、管理に関する工程を省きつつ人件費の削減も実現できます。
製品の追跡がしやすくなる
3つめは、製品の追跡がしやすくなることです。先にも述べたとおり、同じロット番号のものは同一条件下で製造されています。顧客から不良品などのトラブルがあったと報告を受けた場合も、ロット番号がわかれば、どの条件で製造されたものなのかがすぐに確認できます。製造から顧客の手に渡るまでの道筋が明確になるため、多くの商品を出荷する企業にとっては必要不可欠なものだとといえるでしょう。
ロット管理を行うデメリット
このようにメリットの多いロット管理ですが、デメリットも存在します。せっかく便利なロット管理を導入しても、関連業者や社内での管理が正しくおこなわれていないと本末転倒です。そのような場合は、管理ミスや余計な確認工数が発生して、生産性が下がります。このようなトラブルを防ぐためには、社内だけでなく関連業者も含めた全体で同じ認識を持ち、適切に管理することが求められます。
ロット管理を効率的に行う方法
ロット管理を効率的におこなうための方法には、どのようなものがあるのでしょうか。まずは、エクセルなどの表計算ソフトを使用することです。多くの企業には、既に表計算ソフトが導入されているでしょう。そのため、なるべくコストをかけずに管理をおこなうのであればこの方法がおすすめです。しかし、製品の種類が多岐に渡る場合や、数量が非常に多い場合などはミスが多くなってしまうというリスクもあります。
そこで便利なのが、ロット管理をおこなうための専用システムです。この生産管理システムを導入することで、ロット管理を自動化できます。人為的ミスや管理のための手間・時間を大きく削減し、より正確に効率よくロット管理をおこなうことが可能です。
ただし、導入する際には既存のシステムとの連携ができるか、実際に使用する現場の担当者がうまく操作できるかなど、事前に確認しておいた方がよいこともあります。また、少なからずコストはかかるため、導入した場合に得られる恩恵とかかる手間やコストを比べながら、導入を検討しましょう。